Having completed the pass through the ALDs, the next thing I undertook was some cleanup work. The goal was to be able to generate an HDL “group” that contained ALL of the usable HDL pages.
The first step of that was to mark pages I didn’t want as no HDL generation – a relatively recent addition to the application. Then I went through and found all of the switches, and regenerated the affected pages to use update code that used notations in what is ordinarily the signal level fields of the ALD logic blocks associated with the switches (but show up as thinks like DK 2 – meaning switch deck two of a multi-layer rotary switch). I also had to fix up the associated test benches and groups to use the new signal names.
Then I took a shot at generating the whole shebang. I ran into three issues. There were a couple of pages I had skipped that had to do with auto-restart. Dealing with those was simply a matter of marking them to not generate. Next, I ran into an issue with page 13.72.06.1 – which turned out to be a missing page having to do with compute disable cycles for systems with “fast” file (disk) systems. Finally, the ALDs had several cases where the same IBM 1415 console lamp location was specified. I separated them arbitrarily – I don’t seem to have any specific information to help me decide.
Simulation Begins
With those fixes I was able to begin simulation. At first the power on reset wasn’t working right – the 20ms single shot on page 12.65.01.1 wasn’t triggering. This is really a simulation issue, I think – putting in a 30ns wait at the beginning of the simulation dealt with that.
The next issue was that after the reset, pressing the start key did not start the clock – the STOP LATCH stayed on. That in turn kept the clock from starting (ILD Figure 1). That in turn led to noticing that there was no START KEY PULSE when the start key was pressed in the simulation.
Part of the issue was tracked down to the fact that I don’t yet have a console printer emulation in place, and the console contact signals were inconsistent (both C1 and C2 normally closed and normally open signals were false), so I “fudged” it so the cam contact signals would indicate it was not in a cycle. That helped – and was the sort of thing I expect might need attention.
The next issue with the START KEY PULSE signal was that the CONS STOP PRINT COMPLETE signal was 0 – as though it was in the middle of a console stop print out. That was traced down to the Console STARTPRINT switch (page 44.10.01.1) which is unusual in that its N output (usually reserved for an active HIGH signal) is active LOW in this instance. That got me to the point where the START KEY PULSE appeared, and the machine went from Logic Gate B (perhaps it should have been at A?) through Logic Gate E, and which point Master Error was asserted and things stopped.
The error lamps were multitudinous, but the lamp that was first in line in the time line was the B Register Reset Error. The B register gets the contents from memory, and if it does not reset before then, that is an error (otherwise it might return the previous character, or some combination of the previous character and the current one).
Have I ….
By now, if you have been following along, you know what comes next. Yup. Triggers. In particular, card type DEY, used for generating the clock pulses and also for the logic clock (A, B, C, D, ….). Based on the waveforms I saw in the System Fundamentals manual, I had supposed that the AC input signals for set and reset would remain at logic zero until the gate had been turned on, and then pulsed. However, that turned out to be wrong, and it caused the system to advance into Logic Gate B immediate after reset, which caused the missing reset of the B register, among other things. What the system actually does is that the AC Set signal may already be at logic one when the gate on signal comes along – but since the AC Set signal is capacitively coupled, in that case the AC Set does NOT trigger the trigger. That does not happen until, while the gate is on, the AC Set signal transitions from zero to one.
The CPU Executes Its First Instruction
Upon fixing that, a whole bunch of stuff worked. Upon power up restart, the memory address register – the MAR – and the IAR – are already set to 1. So when START is pressed, that is the character read from storage. The instruction I am force feeding to it is the HALT instruction. Then the IAR gets incremented by 1, loaded into the MAR and the following character is read out (and, since I am force feeding it, the character is exactly the same). Since it has a word mark (WM), the system knows that this is a plain halt, and, lo and behold, the system halts.
This success, though, means that I have to go back and test (though not regenerate) all of the pages that use card type SMS_DEY. They should all be fine.
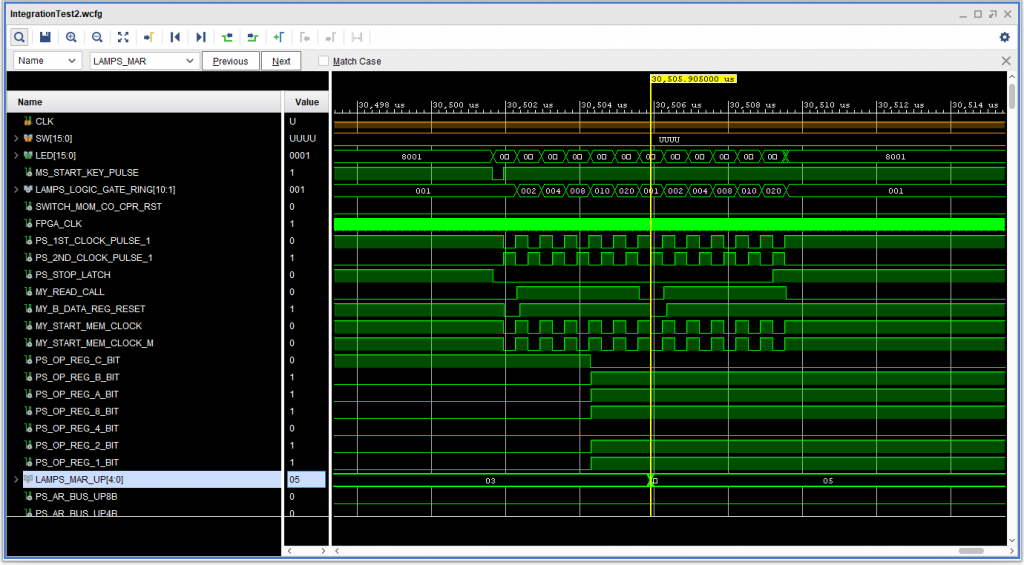
The IBM 1410 executes its first halt instruction
Well, actually, not all of the SMS_DEY usages were fine – there were four test benches with issues. In each case the AC Set or AC Reset signal was changed simultaneously with a collector pull off signal (DCRFORCE in the VHDL) which caused problems given how I coded SMS_DEY.vhdl. Adding a slight delay between the two (which is realistic) fixed the test benches.
Try and Fit onto the FPGA
With that, I made a couple of tweaks to a copy of the Integration2_tb.vhdl to become Integration2_fpga.vhdl and tried to synthesize it. There were a few issues:
- A couple of signals had no drivers because they did not appear as outputs from the sheet: -S F CH FILE OP is used on 12.12.67.1, ostensibly coming from 13.74.04.1 . 13.74.04.1 has the latter ECO (251849 vs. 251824). Also, the card location chart on page 12.12.67.1 does not show the gates that appear on the ALD. For now, I changed 12.12.67.1 to use signal -S FILE OP instead, and changed 13.74.01.1 to output that signal to 12.12.67.1
- Similarly, on the same two pages, 13.47.01.1 outputs -S FILE OP.D CY.EXTENSION but this got mangled into -S FILE OP.DLY.EXTENSION on page 12.12.67.1. It goes to the same gate as #2 above, so it may turn out to be bogus.
- A signal +S BLOCK USE A CH WM is used on page 15.49.02.1, ostensibly originating from page 15.41.12.1. It does not originate there (or anywhere else). Here I changed the signal to “LOGIC ONE” on the destination page, and removed it from the origin page (which has the later ECO, at 253469 vs.251829).
Fixing numbers 2 through 4 was easy, if tedious – I also regenerated and ran the associated test benches. For a little while I thought #1 was just a matter of Vivado not recognizing the my signal named FPGA_CLK was a clock, but found it was indeed recognized. So I dropped that for easier prey…
There were a bunch of references in the Vivado synthesis log complaining about unconnected signal “GROUND”. This was because it appears as an input to sheets – most of them using it for capacitor input, or, in once case, a switch input that the generated HDL ignores in both cases. So, I changed the app to ignore that signal name, as it does with “LOGIC ONE” and “LOGIC ZERO”. Some of the triggers map a signal named GROUND to an *output* so that they can use it as a logic one internally – those I have left — for now. Interestingly, there were two more pages that had this issue that Vivado did NOT call out with a warning – but then failed when I regenerated IntegrationTest2.
The rest of the unconnected inputs I ignored for now – mostly they are cases where a bit vector is input to a page that does not use all the bits. Heck, that really should not be issuing a warning!
Next up was InvShiftRegister.vhdl. The way I had done the shift, one bit was “undefined” for a while – or conceivably could be. I changed the assignment and tested the affected pages again (39.10.01.1, 02.1, 03.1). No page HDL changes required for that. But what was weird was that this exact same assignment is used in ShiftRegister.vhdl, but there it did not generate the warning – but was not called out (see the discussion regarding GROUND, above, where the same kind of thing occurred).
Loop “D” Loops
Another issue that cropped up during synthesis, and became roadblocks when I tried to generate the bitstream for the FPGA involved a couple of apparent combinatorial loops. The application prevents those from being an issue on a single page, but there is no check across pages. Two such loops showed up, one involving +S CONSOLE PRINTER NOT BUSY and the other involving the A Channel WM bit.
It took me a couple of days to learn how to get the tooling to leave enough information in during synthesis so that I could see the problem. Setting the Xilinx Vivado “-flatten_hierarchy” to “none” made things much easier.
The console issue was easy to fix: I just manually inserted a “D” flip flop on page 45.50.08.1. The A Channel one was harder. The first time I looked at the schematic +S A CH NOT WM BIT was in the loop, so I put a “D” flip flop on that signal on page 15.39.08.1. But then the issue moved to +S CH WM BIT, so I put a second flip flop there. But then the issue moved again, this time to +B A CH WM BIT. Looking at the page I quickly saw that these were all fed from the logic block at 4D, so I took out the other two flip flops and put one at the output of block 4D, which cured the problem, both during synthesis and when generating the bitstream.
With normal settings, the design takes up 2858 LUT (look up table) cells and 1628 flip flops. With flatten_hierarcy set to non, it takes up 4001 LUTs and 1805 flip flops (two of which are the ones I added to fix the loops).
Doing some “greps” on the source, I found I had 1200 D flip flops that I had inserted (generated for on-page combinatorial loops — almost all latches), about 128 triggers, not counting the registers needed for implementing one-shots and delays, so the flip flop of 1807 count seems about right.
At one point the flip flop count had been as high as 2046 with a smaller LUT count, but while looking for the combinatorial loop issue I made a change to the VHDL for trigger card type DEY to bring what it thinks of as a DC Set or Reset into the section edge triggered by the 100MHz FPGA clock which actually made things smaller.
The FPGA on the Digilent Nexys 4 is an Artix 7 XCA100T, which can has 15,850 slices – each of which has 8 FF, and which has 101,440 cells. The report says I am using under 6% of the LUT’s and under 1.5% of the flip flops. I hadn’t realized this chip was as big as it is. I should have plenty of room for memory (BRAM with some ROM, too, maybe), channels, console, reader/punch and printer along with a debug core and either or a microBlaze co-processor or an I2C interface (or some such) to connect an Arduino to talk IP to my PC).
A Halting Start
Programming the results into the FPGA, with some code to map the START and COMPUTER RESET buttons sort of works – but unlike the simulation, where all that was necessary after a power on-reset was to press START, here I have to do START, then COMPUTER RESET, then START again – so something is not quite right (and it might be one of the other trigger types needs fixing). [The START KEY PULSE is indeed present during the first START.] Still, it apparently successfully executes the HALT instruction, which is a good step forward.
I also learned about a new tool: the Vivado Integrated Logic Analyzer, which can capture digital signals, and then communicate them back to the PC using a JTAG connection. Handy as heck.
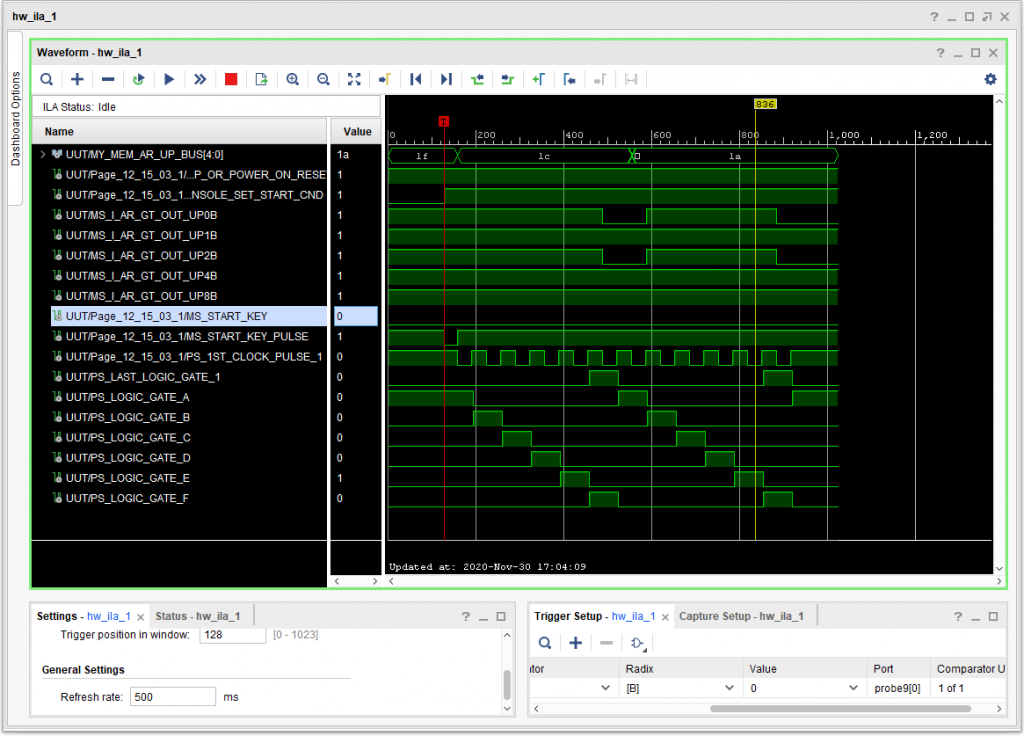